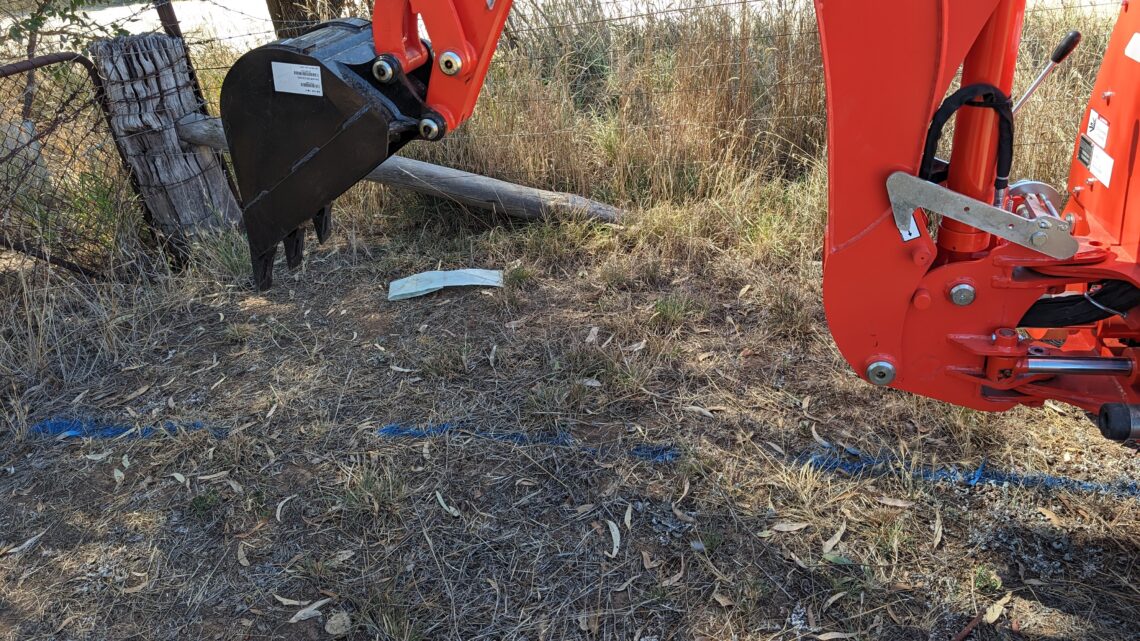
Trenching, Plumbing and Power. Part 1
We purchased a tractor primarily for trenching work related to power and water systems. This investment not only saved us approximately $15,000 on plumbing and electrical expenses but also aids in other tasks around the property, you can see some of the tasks on our to-do list. All of the tasks help justify the investment in the tractor and its attachments.
Dealing with Leaks
This post is about the third task on our “to-do” list, which involves trenching for plumbing and electrical needs. Initially, we planned to start trenching around late March or early April. However, a $600 water bill and a neighbor’s call about a leak in the plumbing passing through their property prompted us to speed up our plans. When we arrived at the property, water was spraying at least 10 feet high. We quickly turned off our mains and hired a local plumber to patch up the leak. After that, we began discussions with the builder’s plumber to plan our next steps.
Unforeseen Location Issues
One aspect we overlooked when purchasing the property was the location of the mains tap. We are responsible for maintaining all plumbing from the mains tap to our property. We discovered that our tap is positioned on the street corner, 340 meters before our property boundary. The plumber assessed the situation and found at least five patch jobs, utilizing a mix of galvanized and plastic plumbing lines. The galvanized parts were rusting, leading to potentially more future leaks. Additionally, only part of the plumbing was visible above ground, leaving us uncertain about the condition of the buried pipes. The plumber recommended decommissioning the old line and installing a new one.
Unexpected Workload
However, this required relocating the trough, which supplied water to our cows since our dam had breached a wall. Consequently, trenching was needed on two properties. The plumber handled the work on the neighbor’s property while we undertook the trenching on ours. This served as the first test of quality and capability for our tractor, trenching to a depth of 600 millimeters and a width of 300 millimeters, over a length of 150 meters (our section of the job). The total length of the line to be laid in this section was estimated to be between 460 and 480 meters, extending near the entrance gate in preparation for connecting to the house site, resulting in an unexpected plumbing line of approximately 800 meters. about 340meters longer than we had planned
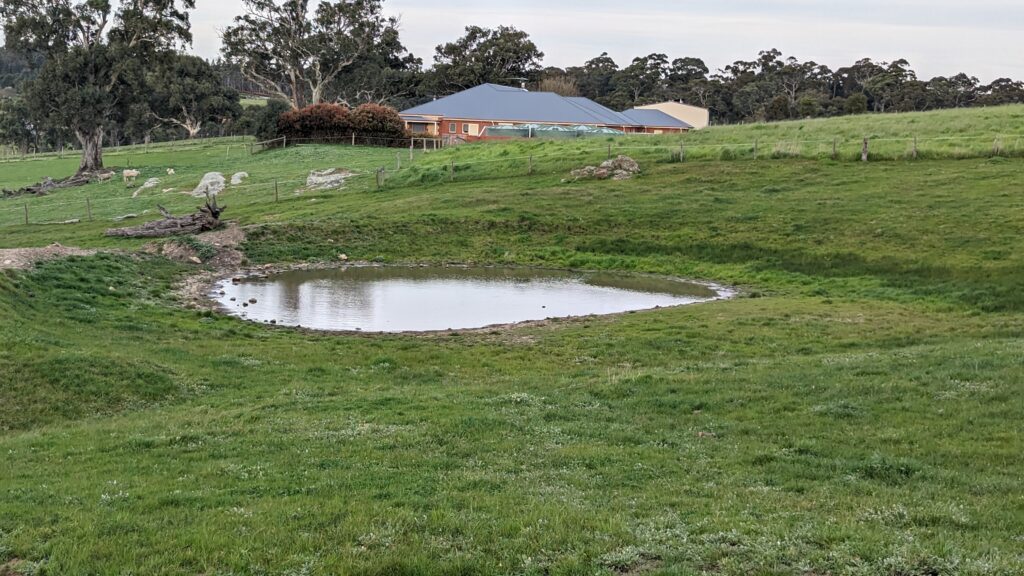
This turned out to be more extensive than initially planned. However, we decided it was better to address it now rather than continually deal with aging, rusting pipes. So, we commenced the trenching work, which took two full days and a couple of late afternoons to complete our 150 meter of the project.
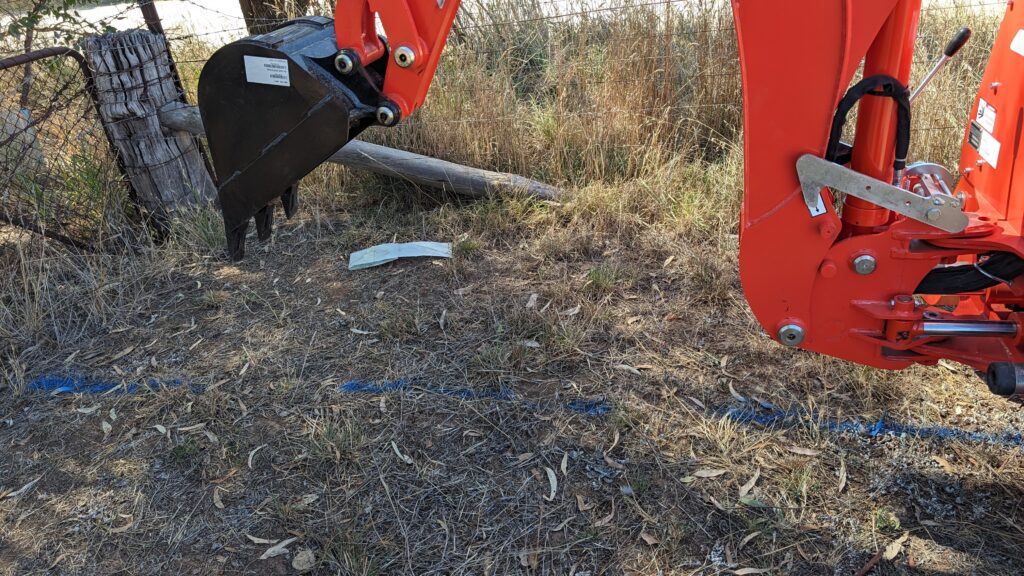
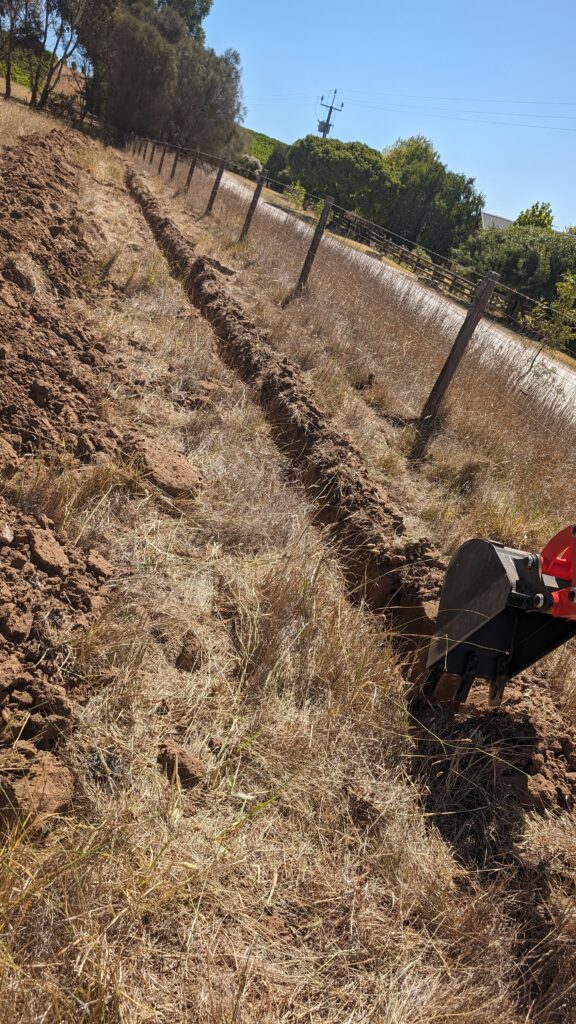
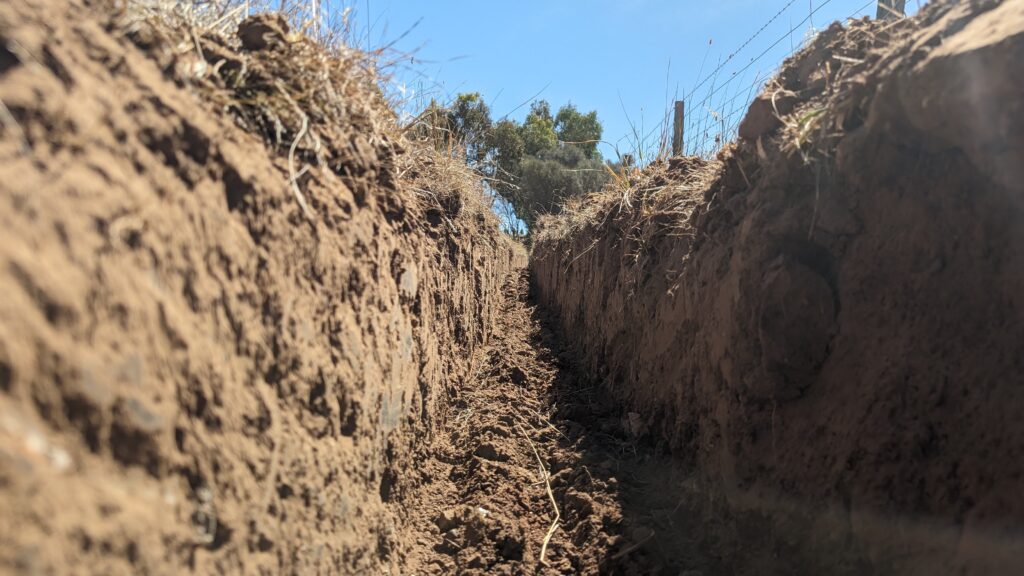
Plumbing in ground
once the trenching was finished the plumber arrived on site to do his part of the project, he disconnected the water and laid the new line, flatten out where the trough was to go and connected a new float and the trough to the mains, putting a tap on so we could disconnect the trough as we see fit. He also put an access pit in for when he will need to run the line up to the house site.
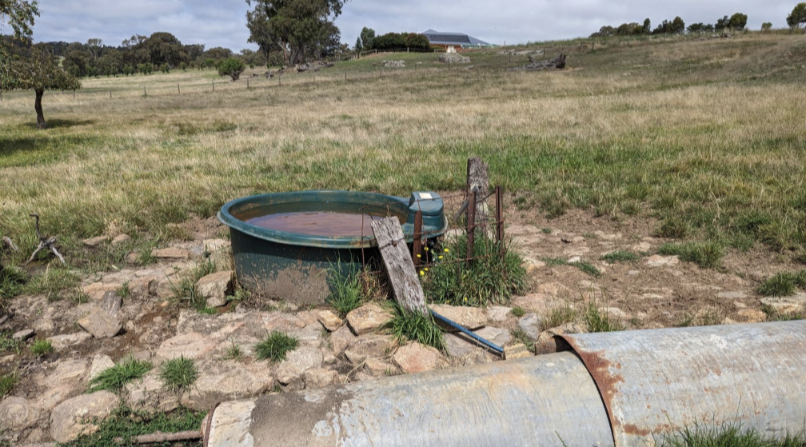
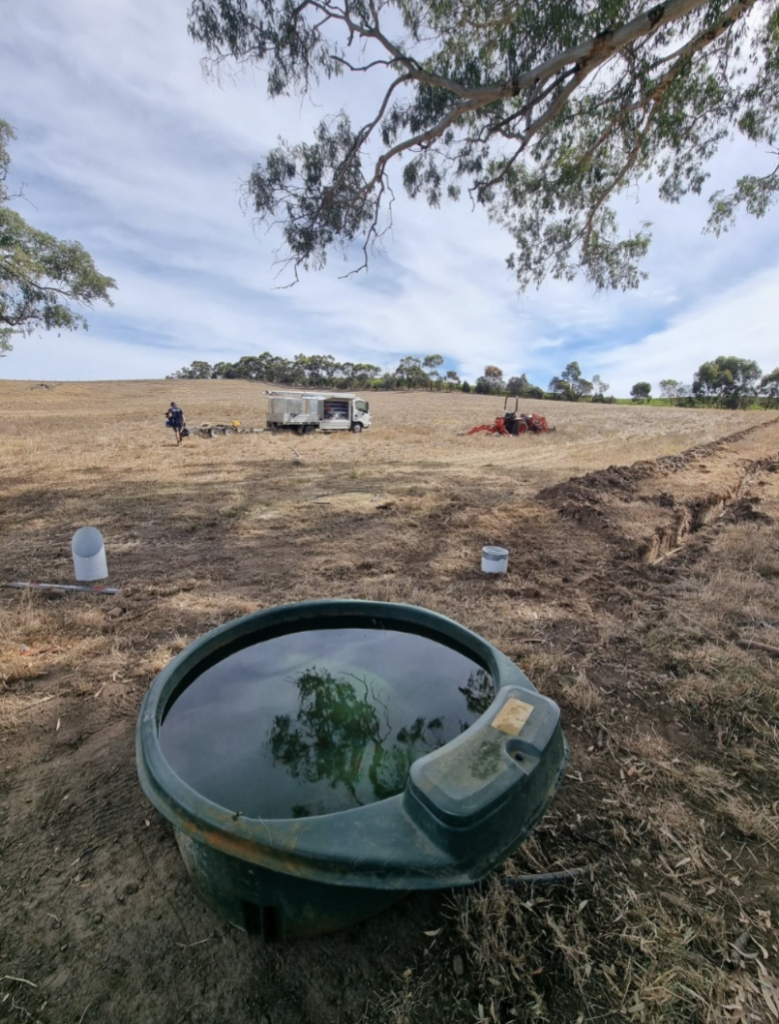
so now the trough is relocated, Lanky will start trenching for the line to be run up to the house. and hopefully in the next couple of weeks that job will be finished.
If you would like to have a look at the tractor we got follow the link here it is a Kioti CK3710
we purchased it from Central hills machinery traders click here to view their website.
